The Implications of TSMC's Global Chip Shortage
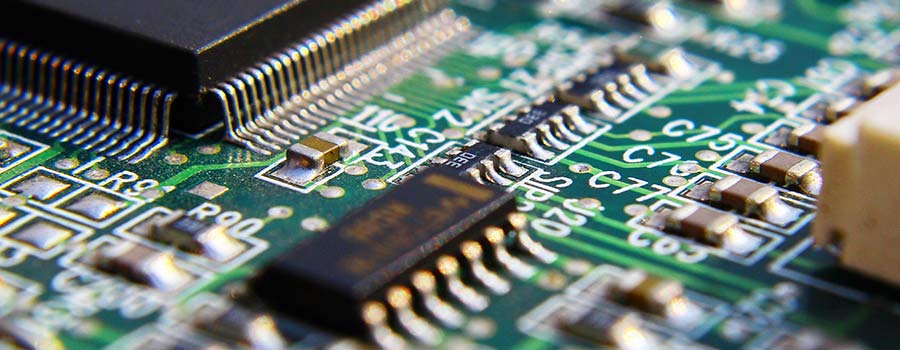
You may not have heard the name TSMC, but the Taiwan Semiconductor Manufacturing Company is working around the clock to help manufacturing and technology companies around the world recover from a global chip shortage, the effects of which has been felt for some time and not just in the industrial computing marketplace.
For instance, whilst AMD and NVidia develop their advanced chip designs, the manufacture of the chips themselves is predominately carried out by TSMC on their behalf. In fact, around 70% of the global supply of such chips come from TSMC factories. With the manufacturers of home computers, mobile phones, automobiles, consoles, tablets and much more are all relying on TSMC product, it's inevitable that lead times for industrial computers will begin to stretch, and continue doing so for some time.
COVID-19 has had an impact in other ways, too. People’s habits have changed during the pandemic — home working, remote meetings — all of this pushes the demand for electronics equipment, putting severe pressure on component manufacturers as they try and meet these requirements. In many areas, with chip manufacture in the centre of the storm, component shortages are now reaching crisis point.
This impact naturally cascades down the supply chain, and fast action is needed by system integrators and OEMs alike if they have any specific computing requirements for deployment within the next 12 months at least. As you can imagine, there is a queue forming rapidly, and early signs suggest that manufacturers may deliver lead times on a first come, first serve basis.
Our aim at Impulse is to face the issues head on to try and mitigate the impacts of the component shortage with a three-pronged approach:
Many customers are already taking a proactive approach and have placed stocking orders to cover specific project requirements. Furthermore, our team are working with them to offer scheduled production and delivery planning that minimises the impact on the customer in terms of cash flow.
For instance, whilst AMD and NVidia develop their advanced chip designs, the manufacture of the chips themselves is predominately carried out by TSMC on their behalf. In fact, around 70% of the global supply of such chips come from TSMC factories. With the manufacturers of home computers, mobile phones, automobiles, consoles, tablets and much more are all relying on TSMC product, it's inevitable that lead times for industrial computers will begin to stretch, and continue doing so for some time.
A perfect storm
Countless factory workers furloughed due to COVID-19, US sanctions levied on China by the Trump administration, political unrest between Taiwan and China, a ship stuck in the Suez canal, even a drought in mainland Taiwan — it is a perfect storm of issues that couldn't have been designed more efficiently to disrupt the manufacturing and supply chain of chips and computing components across the globe.COVID-19 has had an impact in other ways, too. People’s habits have changed during the pandemic — home working, remote meetings — all of this pushes the demand for electronics equipment, putting severe pressure on component manufacturers as they try and meet these requirements. In many areas, with chip manufacture in the centre of the storm, component shortages are now reaching crisis point.
Fast action is needed for upcoming projects
Our global industrial computing partners are as powerless as every other manufacturer relying on the supply of TSMC's chips, with price increases, and lead times being stretched left, right and centre. Despite increases in production by component manufacturers, and additional funds being pumped into bolstering the infrastructure surrounding this manufacturing process, many industry experts are suggesting it will take until the end of 2022 to get back to a level where supply can meet demand.This impact naturally cascades down the supply chain, and fast action is needed by system integrators and OEMs alike if they have any specific computing requirements for deployment within the next 12 months at least. As you can imagine, there is a queue forming rapidly, and early signs suggest that manufacturers may deliver lead times on a first come, first serve basis.
Impulse is here to help
Over the last 25 years of Impulse's trading, we have seen a number of shortages such as these. You may remember the credit crunch of 2008, where banks held money and global component shortages pushed lead times out to over 16 weeks in most cases. Impulse reacted quickly at the time by investing in stock and working with the supply chain, mitigating the impact to customers and ensuring minimal supply issues for affected projects. This is no different, and our experience, stability, and relationships with manufacturers allow us to prepare once more.Our aim at Impulse is to face the issues head on to try and mitigate the impacts of the component shortage with a three-pronged approach:
- INVESTMENT IN STOCK AND SYSTEMS
Firstly, we have immediately tripled our normal investment in free-stock across many lines, which is helping us to meet demand for our fast-moving goods. The increased warehouse space in our new facility is certainly being put to good use.
In recent months we have also increased our investments in software tools with the aim of improving visibility and reporting on our purchasing, production, and stock handling capabilities.
- WORKING IN UNISON WITH THE SUPPLY CHAIN
As the main official UK distributor and partner for many of our manufacturing partners, we have a direct relationship with the factories. These relationships help us obtain fast and accurate daily updates and allow us to work closely with the manufacturers to consolidate our customers’ orders and provide additional visibility of demand so the manufacturers can plan their own production accordingly.
The close links with our supply chain partners, hardware manufacturers and component suppliers are also helping us to secure stocks of our fast-selling lines.
- PROACTIVELY ENGAGING WITH CUSTOMERS
The most important factor, however, has been our proactive approach to discussing things with our customers. Our account managers are working hard to gain as much visibility as possible of customer demand. Obtaining customer forecasts has meant we can guide them through the current issues with minimal disruption.
Many customers are already taking a proactive approach and have placed stocking orders to cover specific project requirements. Furthermore, our team are working with them to offer scheduled production and delivery planning that minimises the impact on the customer in terms of cash flow.